Picking the right finish for pipework on your boat depends on a few factors. Learn more about making the best decision.
Whether specifying equipment on a new boat or ordering an aftermarket aluminum wake tower or T-top, you might need to choose a finish for the pipework. The decision will hinge on your taste in aesthetics, where you plan to boat, and more. When it comes to cost, each finish is roughly comparable. Here’s what’s available.
Anodized
Anodizing is accomplished by immersing aluminum into an acid electrolyte bath and passing an electric current through it to convert the metal surface into a corrosion-resistant finish. Anodizing can be done in various colors, but most marine pipework is clear-anodized. “It is a good choice for those who boat in salt or brackish water,” says Sabrina Donaldson, manager of Big Air Towers. It stands up well to rough use and does not show fingerprints, she points out. However, if it is scratched, anodizing cannot be easily repaired, and the damaged area can foster corrosion.
Polished
Polishing raw aluminum results in a chrome-like surface that shines more brightly than any other finish, and some boaters prefer this look, especially if it matches other chrome or polished-aluminum equipment on their boats. However, it does not offer the same corrosion resistance as other finishes, and so polished-aluminum towers are best-suited for use in fresh water. “It also requires more maintenance—regular buffing with aluminum polish—to keep the bright, shiny look,” says Donaldson. It also shows fingerprints, and the raw aluminum is slightly more vulnerable to scratches than other finishes, but many small scratches and mars can be buffed out.
Painted
One of the few fabricators to offer painted finishes is Roswell Marine. Its automotive-style, glossy painted finishes feature an underbarrier achieved with a process known as Chem Dip prior to applying primer and paint. “This is where the real magic happens,” says Darrick Wilson, chief of design for Roswell. Once the pipework surfaces are perfectly smooth and thoroughly cleaned, the Chem Dip process produces a corrosion-resistant layer akin to anodizing, Wilson explains. The paint is baked in a booth to create a durable finish that stands up to corrosion in marine environments. Painting allows for a multitude of color choices, and if a finish is scratched or chipped, repairs are easier to achieve than with any other finish.
Raptor-Coated
Roswell Towers offers a unique finish from Raptor coatings that creates a thick, corrosion-resistant urethane layer that is extremely durable. It will not fade, scratch, crack or break down, according to Raptor. “Think in terms of spray-on bed liner for trucks,” Wilson says. “Roswell makes it available upon customer request.” It is available in 30 different shades to match a boat’s color scheme, but has very little gloss and sports an orange-peel texture, so it gives the boat a rugged appearance.
Read Next: How to Choose the Right Tow Tower
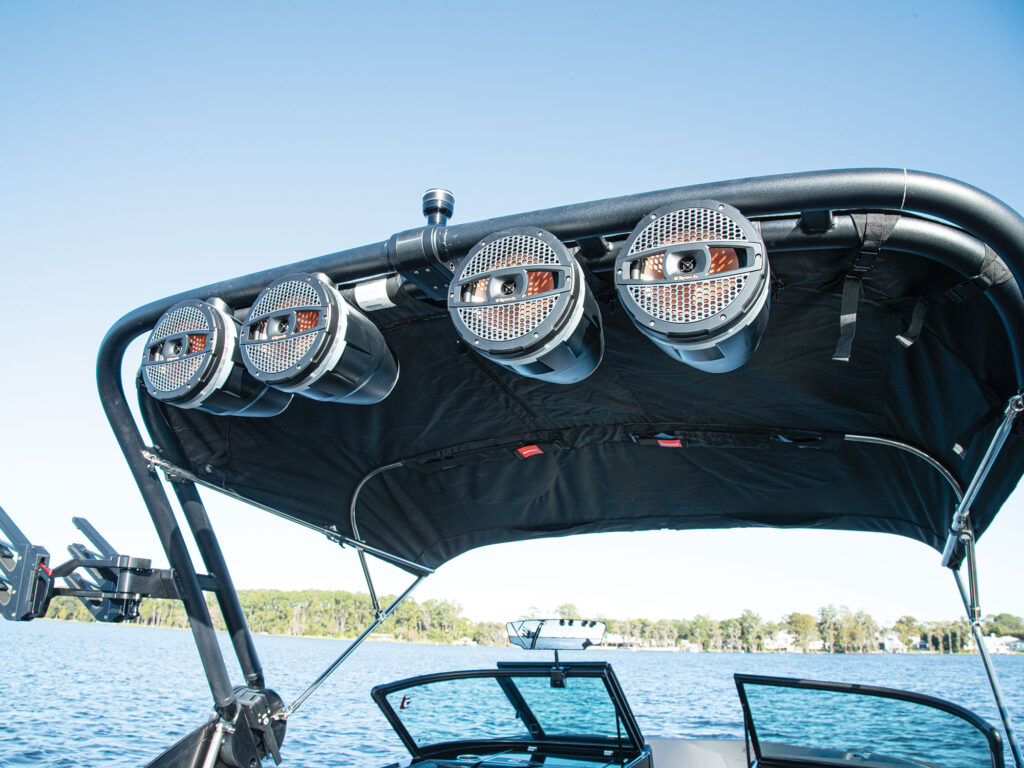
Pipework finishes often combine durability and aesthetics. Courtesy MasterCraft
Powder-Coated
Powder-coating is created by an electric charge that causes a dry powder to adhere to the aluminum. It is then baked to achieve a smooth, semigloss coating. It’s available in virtually any color to match the boat. It’s more durable than paint and is highly corrosion-resistant, making it a popular finish for pipework. In the aftermarket, black- and white-powder-coated towers and T-tops are the most common standard offerings, with custom colors available for an upcharge. Maintenance—wipe down with mild soap and water after each trip—is low. If a chip or scratch does occur, matching paint can be used to affect a decent repair.